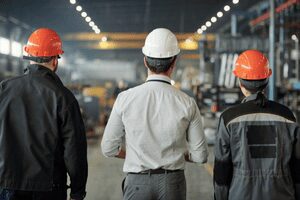
Balancing shift coverage and overtime in manufacturing plants can be challenging for employers. Inadequate shift coverage can lead to delays in production, increased overtime costs, and employee burnout. In contrast, overuse of overtime can result in increased labour costs, decreased productivity, and lower employee morale. To effectively manage these issues, employers must implement strategies and tools that can help them ensure adequate shift coverage and prevent excessive overtime use.
General Scheduling Problems within Manufacturing Plants
Balancing shift coverage and overtime is a significant challenge for many employers. This is particularly in manufacturing plants where production schedules can be unpredictable and labour-intensive. Failing to balance shift coverage and overtime properly can result in decreased productivity, lower employee morale, and increased labour costs. Here are some common problems employers face in balancing shift coverage and overtime in manufacturing plants.
INADEQUATE SHIFT COVERAGE:
One of the employers’ most significant problems is ensuring adequate shift coverage to meet production demands. This can be challenging, mainly when unpredictable production schedules require considerable labour. Failing to provide good shift coverage can lead to delays in production, increased overtime costs, and employee burnout.
Inadequate shift coverage can occur when insufficient workers are available to meet production demands. This problem can be particularly acute in manufacturing plants as production schedules can be unpredictable and labour-intensive. For example, a plant may require more workers during peak production periods or when a large order comes in. Having enough workers available during these periods can increase productivity and labour costs.
According to a National Bureau of Economic Research study, understaffing can lead to decreased productivity, decreased employee satisfaction, and increased absenteeism. On the other hand, adequate staffing can lead to increased productivity and higher employee morale. In addition, a survey by the Society for Human Resource Management found that 41% of companies reported experiencing scheduling difficulties due to inadequate shift coverage.
OVERUSE OF OVERTIME:
Another problem employers face is overusing overtime to meet production demands. While overtime can be a valuable tool for managing production schedules, overusing can result in increased labour costs, decreased productivity, and lower employee morale. Moreover, there are legal and regulatory requirements around overtime, and employers who violate these requirements may face penalties and fines.
Overuse of overtime can be a problem in manufacturing plants when production demands are high and insufficient workers are available to meet those demands. Overtime can be a valuable tool for managing production schedules. However, overusing can result in increased labour costs, decreased productivity, and lower employee morale. Furthermore, there are legal and regulatory requirements around overtime, and employers who violate these requirements may face penalties and fines.
According to the Bureau of Labor Statistics, the average manufacturing worker earned $20.56 per hour in 2020. However, the average overtime rate was $30.84 per hour. This means employers are paying 1.5 times the regular hourly rate for every overtime worked. In addition, overuse of overtime can lead to employee burnout, resulting in decreased productivity, increased absenteeism, and higher employee turnover.
To address these problems, employers can use various strategies and tools to balance shift coverage and overtime in manufacturing plants effectively. For example, implementing automated scheduling systems can ensure enough workers are available to meet production demands. These systems can also help employers monitor employee work hours and avoid violations of overtime regulations. Furthermore, training supervisors and employees on effective scheduling practices can help ensure that all workers are scheduled properly and efficiently. Employers can improve productivity, reduce labour costs, and enhance employee morale and satisfaction by proactively balancing shift coverage and overtime.
EMPLOYEE BURNOUT:
Employee burnout is a major concern for employers in manufacturing plants. Inadequate shift coverage and overuse of overtime can take a toll on workers’ physical and mental well-being. Burnout can lead to decreased productivity, increased absenteeism, and higher employee turnover. All of which can have a significant impact on an employer’s bottom line.
According to a survey by Kronos Incorporated, 95% of HR leaders believe that employee burnout is sabotaging workforce retention. The survey also found that employee burnout was responsible for up to 50% of workforce turnover.
In manufacturing plants, where the work is often labour-intensive and physically demanding, the risk of employee burnout is particularly high. If employers do not provide adequate rest breaks or schedule enough workers to cover all shifts, employees may become fatigued and stressed. This can lead to burnout. In addition, excessive use of overtime can result in long work hours. This would leave employees with little time to rest and recharge.
For example, a study by the National Institute for Occupational Safety and Health (NIOSH) found that long work hours and extended workweeks were associated with increased risks of injury and illness among manufacturing workers. The study found that employees who worked more than 12 hours per day or more than 60 hours per week had a significantly higher risk of injury and illness than those who worked shorter hours.
INEFFICIENT SCHEDULING PROCESSES:
Lack of visibility into employee availability and qualifications can lead to scheduling errors and lower productivity.
In manufacturing plants, it can be difficult to keep track of employee availability and qualifications. Especially if there are a large number of employees working across multiple shifts. Without a clear understanding of which employees are available to work and which ones have the necessary skills and certifications for a given task, employers may inadvertently schedule the wrong employees, resulting in lost productivity and increased costs.
According to a study by Workforce Insight, 50% of employers cite the inability to accurately forecast staffing needs as one of their biggest workforce management challenges. The study also found that inaccurate scheduling can result in up to 3% of a company’s annual revenue being lost due to reduced productivity and higher labour costs.
For example, imagine a manufacturing plant that needs to produce a certain number of widgets each day. If the plant manager does not have an accurate view of employee availability and qualifications, they may schedule workers who are not properly trained or who are unable to work the required shifts. Consequently, leading to production delays and increased costs.
COMPLIANCE ISSUES:
Finally, employers must comply with legal and regulatory requirements around shift coverage and overtime, such as the Fair Labor Standards Act (FLSA) and state-specific labour laws. Failure to comply with these requirements can result in penalties, fines, and damage to the company’s reputation.
Compliance with labour laws is a critical consideration when balancing shift coverage and overtime in manufacturing plants. Employers must comply with federal and state regulations related to minimum wage, overtime, and rest breaks, as well as specific industry regulations related to workplace safety and health. Failure to comply with these regulations can lead to penalties and fines, as well as decreased employee morale and productivity.
According to the Department of Labor, employers paid $322 million in back wages in 2020 to more than 330,000 workers due to violations of minimum wage and overtime regulations. In addition, employers who violate workplace safety regulations may face penalties of up to $13,653 per violation, and repeat offenders may face penalties of up to $136,532 per violation.
How Celayix can help balance shift coverage and overtime in manufacturing plants
Balancing shift coverage and overtime in manufacturing plants can be challenging for employers. Inadequate shift coverage can lead to delays in production, increased overtime costs, and employee burnout. In contrast, overuse of overtime can result in increased labour costs, decreased productivity, and lower employee morale. To effectively manage these issues, employers must implement strategies and tools that can help them ensure adequate shift coverage and prevent excessive overtime use.
This is where Celayix comes in. Celayix is a leading provider of employee scheduling and workforce management solutions to help employers balance shift coverage and overtime in manufacturing plants. Our advanced scheduling and time-tracking software can help automate the scheduling process and ensure enough workers are available to meet production demands. Additionally, our software can help employers monitor employee work hours and avoid violations of overtime regulations, thus reducing the risk of legal penalties and fines.
Celayix’s scheduling software is customizable and can be tailored to meet the specific needs of different manufacturing plants. For example, it can be programmed to account for peak production periods, seasonal fluctuations in demand, and specific skill sets required for certain jobs. This can help employers schedule workers more efficiently and effectively, reducing the risk of inadequate shift coverage and overuse of overtime.
FINAL SAY
Overall, with the help of Celayix’s scheduling and workforce management solutions, employers can improve productivity, reduce labour costs, and enhance employee morale and satisfaction in manufacturing plants. By taking a proactive approach to balancing shift coverage and overtime, employers can ensure that their workforce is operating at peak efficiency, which is essential for the success of any manufacturing operation.